As semiconductor technologies become more complex, so do the demands on the materials and processes used to manufacture them. From high-frequency RF applications to micro-scale thermal insulation, component performance is no longer just about design — it’s about precision, thermal resilience, and clean integration into production workflows.
Ceramic materials are increasingly favored for these critical components due to their exceptional thermal, dielectric, and mechanical properties. However, conventional ceramic manufacturing methods (injection molding, CNC machining, pressing) often introduce limitations in geometry, long lead times, and high
tooling costs — all of which conflict with the fast-paced innovation cycles of the electronics industry.
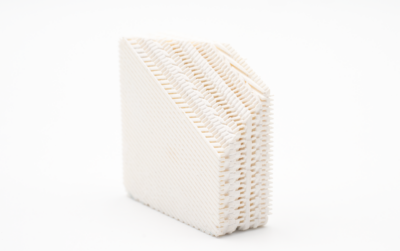
This is where ceramic additive manufacturing steps in, particularly DLP (Digital Light Processing) technologies that enable complex, high-precision parts to be produced without molds or extensive post-machining.
Among the available technical ceramics, alumina (Al₂O₃) stands out as the most commonly used — thanks to its versatility, high purity, and proven performance in both prototyping and end-use applications.
At Prodways Machines, we’ve translated this potential into real production capability with our Alumina A100 and A110 resins, developed in collaboration with Tethon 3D and fully optimized for our CERAM PRO 3D printers.
What Alumina Delivers — In Real Terms
1. Prints complex geometries with no warping or distortion — perfect for insulators, filters, or RF guides.
2. Withstands high temperatures without losing dimensional or mechanical stability.
3. Ultra-fine resolution (150 µm features, 50 µm layer thickness) — critical for small, intricate parts.
4. Speeds up prototyping and pre-series production — no molds, no tooling delays, no compromise.
Why It Works for Semiconductor Applications
1. Consistent quality — highly repeatable printing and sintering process.
2. Design agility — test, modify, and reprint components within hours.
3. Lower cost and lead time for small batches or complex part geometries.
4. Proven compatibility — based on alumina, the industry’s most trusted ceramic.
A100 vs A110: Which Should You Use?
Resin | Ideal Use | Key Benefits |
---|---|---|
Alumina A100 | Small to mid-size parts, high detail | Smooth surface finish, precise features |
Alumina A110 | Larger or complex parts | Higher green strength, easier handling, better sintering for bulk |
Powered by CERAM PRO: Maximum Output, Minimum Risk
CERAM PRO printers are engineered specifically for ceramic DLP printing. When paired with Alumina A100 or A110, you get dimensional accuracy, excellent repeatability, and seamless integration into your production workflows.
Ready to Move Forward?
3. Complete the form to download the full datasheet